Question 1.2: Mechatronic Systems—Design of a Formula Lightning Electric R...
Mechatronic Systems—Design of a Formula Lightning Electric Race Car
The Formula Lightning electric race car competition is an interuniversity² competition project that has been active since 1994. This project involves the design, analysis, and testing of an electric open-wheel race car. A photo and the generic layout of the car are shown in Figures 1.3 and 1.4. The student-designed propulsion and energy storage systems have been tested in interuniversity competitions since 1994. Projects have included vehicle dynamics and race track simulation, motor and battery pack selection, battery pack and loading system design, and transmission and driveline design. This is an ongoing competition, and new projects are defined in advance of each race season. The objective of this competitive series is to demonstrate advancement in electric drive technology for propulsion applications using motorsports as a means of extending existing technology to its performance limit. This example describes some of the development that has taken place at the Ohio State University. The description given below is representative of work done at all of the participating universities.
ــــــــــــــــــــ
{ }^{2} Universities that have participated in this competition are Arizona State University, Bowling Green State University, Case Western Reserve University, Kettering University, Georgia Institute of Technology, Indiana University—Purdue University at Indianapolis, Northern Arizona University, Notre Dame University, Ohio State University, Ohio University, Rennselaer Polytechnic Institute, University of Oklahoma, and Wright State University.
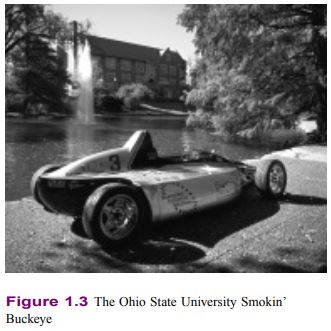

Learn more on how we answer questions.
Design Constraints:
The Formula Lightning series is based on a specification chassis; thus, extensive modifications to the frame, suspension, brakes, and body are not permitted. The focus of the competition is therefore to optimize the performance of the spec vehicle by selecting a suitable combination of drivetrain and energy storage components. In addition, since the vehicle is intended to compete in a race series, issues such as energy management, quick and efficient pit stops for battery pack replacement, and the ability to adapt system performance to varying race conditions and different race tracks are also important design constraints.
Design Solutions:³
Teams of undergraduate aerospace, electrical, industrial, and mechanical engineering students participate in the design of the all-electric Formula Lightning drivetrain through a special design course, made available especially for student design competitions.
In a representative course at Ohio State, the student team was divided into four groups: battery system selection, motor and controller selection, transmission and driveline design, and instrumentation and vehicle dynamics. Each of these groups was charged with the responsibility of determining the technology that would be best suited to matching the requirements of the competition and result in a highly competitive vehicle.
Figure 1.5 illustrates the interdisciplinary mechatronics team approach; it is apparent that, to arrive at an optimal solution, an iterative process had to be followed and that the various iterations required significant interaction between different teams.
To begin the process, a gross vehicle weight was assumed and energy storage limitations were ignored in a dynamic computer simulation of the vehicle on a simulated road course (the Cleveland Grand Prix Burke Lakefront Airport racetrack, site of the first race in the series). The simulation employed a realistic model of the vehicle and tire dynamics, but a simple model of an electric drive-energy storage limitations would be considered later.
The simulation was exercised under various scenarios to determine the limit performance of the vehicle and the choice of a proper drivetrain design. The first round of simulations led to the conclusion that a multispeed gearbox would be a necessity for competitive performance on a road course, and also showed the need for a very high performance AC drive as the propulsion system. The motor and controller are depicted in Figure 1.6.
Once the electric drive had been selected, the results of battery tests performed by the battery team were evaluated to determine the proper battery technology, and the resulting geometry and weight distribution of the battery packs. With the preferred battery technology identified (see Figure 1.7), energy criteria was included in the simulation, and lap times and energy consumption were predicted. Finally, appropriate instrumentation was designed to permit monitoring of the most important functions in the vehicle (e.g., battery voltage and current, motor temperature, vehicle and motor speed). Figure 1.8 depicts the vehicle dashboard.Table 1.2 gives the specifications for the vehicle.
Table 1.2 Smokin’ Buckeye specifications
Drive system:
Vector controlled AC propulsion model 150
Motor type: three-phase induction, 150 \mathrm{~kW}
Weight: motor 100 \mathrm{lb}, controller 75 \mathrm{lb}
Motor dimensions: 12-in diameter, 15-in length
Transmission/clutch:
Webster four-speed supplied by Taylor Race Engineering Tilton metallic clutch
Battery system:
Total voltage: 372 \mathrm{~V} (nominal)
Total weight: 1440 \mathrm{lb}
Number of batteries: 31
Battery: Optima spiral-wound lead-acid gel-cell battery
Configuration: 16 battery packs, 12 or 24 \mathrm{~V} each
Instrumentation:
Ohio Semitronics model EV1 electric vehicle monitor
Stack model SR 800 Data Acquisition
Vehicle dimensions:
Wheelbase: 115 in
Total length: 163 in
Width: 77 in
Weight: 2690 \mathrm{lb}
Stock components:
Tires: Yokohama
Chassis: 1994 Stewart Racing Formula Lightning
Springs: Eibach
Shocks: Penske racing coil-over shocks
Brakes: Wilwood Dynalite II
Altogether approximately 30 students from different engineering disciplines participated in the initial design process. They received credit for their effort either through the course-ME 580.04, Analysis, Design, Testing and Fabrication of Alternative Vehicles-or through a senior design project. As noted, interaction among teams and among students from different disciplines was an integral part of the design process.
Comments: The example illustrates the importance of interdisciplinary thinking in the design of mechatronics systems. The aim of this book is to provide students in different engineering disciplines with the foundations of electrical/electronic engineering that are necessary to effectively participate in interdisciplinary engineering design projects. The next 17 chapters will present the foundations and vocabulary of electrical engineering.
ــــــــــــــــــــ
{ }^{3} K. Grider, G. Rizzoni, “Design of the Ohio State University electric race car,” SAE Technical Paper in Proceedings, 1996 SAE Motorsports Conference and Exposition, Dearborn, MI, Dec.10-12, 1996.



